化学工場の自動化、IoT化を実現!DX実現方法とプロセスオートメーションを解説
化学工場では一般的に自動化、機械化が進めやすく生産設備、装置の大型化によりスケールメリットを得やすいとされています。
しかし、化学プラントの生産工程は複雑で原料品、中間財、最終製品など多岐にわたる製品があります。
プロセス産業である化学業界では工場の自動化技術としてプロセスオートメーション(プロセス制御)がよく導入されています。
プロセスオートメーション(プロセス制御)とは
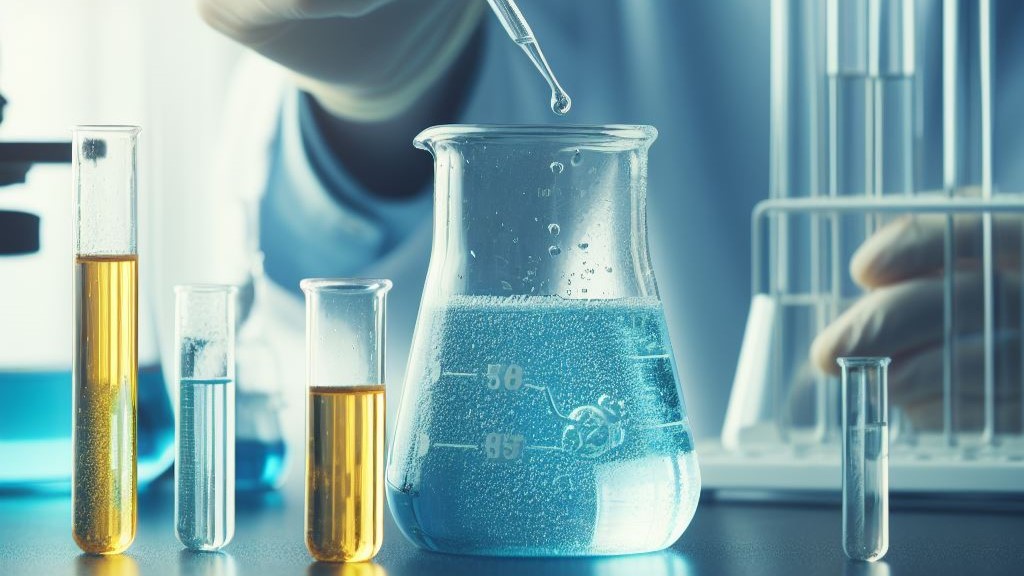
プロセスオートメーションとは素材産業の製造工程や工場の制御、自動化のことを指しています。
原料に熱や圧力を加え加工素材となる製品を製造します。例として牛乳からチーズを作ったり、鉄鉱石から鉄を作ったり、石油からナフサを作るなどが挙げられます。
これらの工程では製造工程で化学反応を利用するため、生産システムのデータだけではなく、温度や圧力、湿度、流量などのアナログデータも取得し適切に制御する必要があります。このような制御を通称してプロセス制御と呼びます。
またプロセスオートメーションはロボットなどを用いた生産ラインと違い生産を一時中断することができません。プロセスオートメーションの設備を強制停止させても始まった化学反応を止めることができないためです。そのため高度なセンシング技術と細かなソフトウェア技術が要求されています。
化学工場におけるシステム導入事例
化学工場での具体的なシステム導入事例を紹介します。
化学プラント生産工程内でIoTを用いた自律制御と老朽化対策システムの導入
化学プラント設備は天候による気温や湿度の変化などの外部から影響を受けやすいため、現場の作業員がバルブを調整する必要がありました。
この作業を削減するためにプラント設備が外部情報をセンシングし、ソフトウェアが自律制御をすることで省人化が実現可能になります。
さらに、各駆動機器に累計稼働時間や通電電流を測定、計算するセンシング機器を取り付ける事でプラント設備が異常停止してしまう前に対策することが可能になります。
思わぬトラブルでプラント設備が停止してしまう前に対策できることで生産工程を崩すことなく運用可能になります。
爆発性のある危険環境下において防爆仕様のロボットシステムを実現
化学工場では危険な薬物を取り扱ったり、爆発性雰囲気を持ったりと危険度の高い環境があります。危険環境下においても機器の故障や事故、製品品質を損なわないためにはロボットシステム全体を防爆仕様にする必要があります。
ロボットシステムだけではなく、製品の入荷から出荷までの工程の中で危険物搬送の自動化や複雑作業の自動化も実現可能です。既設の基幹システムに新たにロボットシステムを通信させることで工場全体のネットワークを実現し、完全無人工場を実現可能になります。
粉体混合ブレンダーと自動搬送システムの導入
樹脂粉末、火薬、ウラン粉末、農薬、粉末塗料などの製造過程で粉体混合機が活用されています。
当社の混合機は容器回転型を採用しており、粉体を可能な限り破壊せずに混合可能です。また、容器を自在に脱着できる構造としているため混合用だけではなく容器を移し替えることなく保管することが可能です。
粉体混合機への容器のセットや混合後の容器の取出し。搬送をAGVやAMRを用いて自動化することで完全無人の粉体混合システムが実現可能になります。
関連コンテンツ
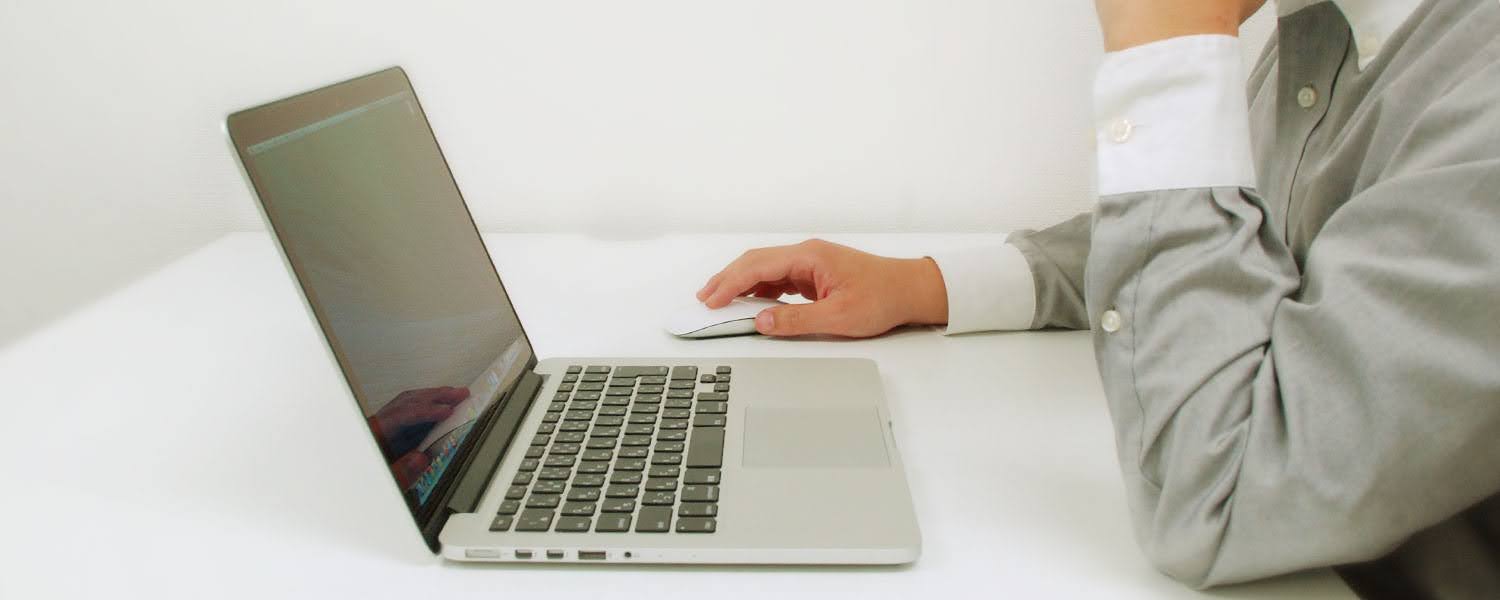
CONTACT
ご依頼及び業務内容へのご質問などお気軽にお問い合わせください